Introducción
Cuando se considera el proceso integral de formular, producir y entregar un alimento para satisfacer los requerimientos nutricionales de las aves, se generan tres tipos diferentes de alimentos: el que formula el nutricionista, el que produce la fábrica de alimento y el que se come finalmente el animal. Esto significa que nunca podemos estar totalmente seguros de los nutrientes que realmente está consumiendo el ave. La forma más apropiada para que lo que esté comiendo el ave se aproxime a la formulación que le hemos diseñado es conociendo muy bien las materias primas que se están comprando; teniendo un buen manejo del almacenamiento de esos ingredientes; una manufactura adecuada y una proceso eficiente de alimentación.
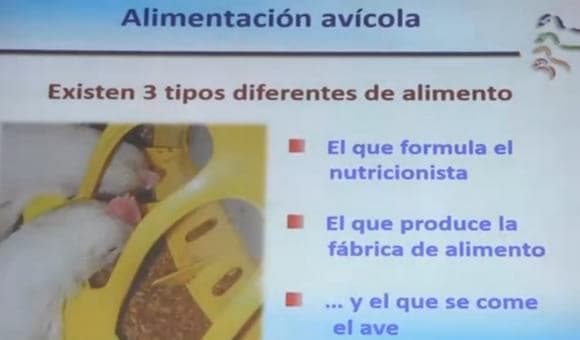
La manufactura adecuada del alimento implica una estrecha relación del nutricionista con el personal de la fábrica de alimento. Esta relación permite por un lado asegurar que el alimento sea fabricado de acuerdo con las especificaciones sugeridas en la formulación y por otro, para tomar decisiones en caso de alteraciones o errores durante la manufactura.
El personal de la fábrica de alimento normalmente conoce muy bien el proceso integral de manufacturar el alimento; sin embargo es imprescindible que el nutricionista integre la respuesta de las aves a las diferentes condiciones de la fabricación para optimizar el desempeño o evitar problemas productivos. Existen ciertas etapas en la fabricación del alimento que tienen un impacto directo en la productividad de las aves donde el nutricionista debiera tener una activa participación.
Recepción y almacenamiento de las materias primas
Debido a la escasez y consecuentemente al alto costo de las materias primas en los últimos años, es más frecuente encontrar lotes de inferior calidad debido a diluciones de la composición nutritiva por adulteraciones o por un exceso de humedad, que muchas veces conllevan una contaminación fúngica, lo que puede derivar en intoxicaciones por la presencia de micotoxinas. Todavía existen problemas con lotes de harina de soya mal procesados que generan graves problemas de desempeño junto con camas húmedas y deterioro del cojinete plantar cuando la cocción no se realizó adecuadamente. En el caso de sobrecalentamiento, que es menos común, la situación no es tan seria y se puede contrarrestar adicionando una cantidad extra de lisina o de lisina y metionina a la ración.
Todo lo anterior hace necesario que cuando se reciban los ingredientes exista una inspección visual de cada uno de ellos, una adecuada toma de muestras y un programa de análisis simples de realización inmediata (humedad, densidad, microscopía) y otros específicos para cada ingrediente, que siempre debieran considerar la fuente o proveedor. El Dr. Dale en su publicación In vitro and in vivo procedures in quality control programmes presenta una excelente orientación sobre los análisis que debieran realizarse para cada materia prima.
Es importante tener en cuenta que en la compra de materias primas y especialmente de aditivos debe existir una supervisión técnica nutricional que oriente correctamente al personal de compras.
La calidad de los ingredientes nunca mejora a través del tiempo; por lo tanto durante el almacenaje se debe tratar de minimizar su deterioro. La proliferación de hongos y la consecuente contaminación con micotoxinas son los principales problemas durante el almacenaje. Los factores más críticos que aumentan estos problemas son la humedad, la cual no debiera ser mayor de 14 - 14.5% en los granos ni mayor de 10.5 - 11% en las semillas oleaginosas; la presencia de insectos y/o roedores que destruyen la integridad del grano y aumentan la cantidad de finos; y el tiempo de almacenaje.
Varios aditivos, especialmente vitaminas y enzimas, requieren de cuidados de almacenaje relacionados con temperatura y hay que tener presente, que al igual que los medicamentos, tienen fecha de expiración.
Molienda y pesaje
Existen dos tipos generales de diseño de fábricas de alimento: las que tienen la molienda antes de mezclar y las que muelen después de mezclar. Si la molienda es anterior al mezclado, entonces este proceso se puede manejar en forma independiente y se pueden tener diferentes tamaños de partículas dependiendo del tipo de alimento a fabricar. La única desventaja de este sistema es que requiere de más capacidad de almacenaje (silos) para los ingredientes molidos.
El tamaño de partícula es de gran importancia en las aves, pues su capacidad gustativa y olfativa es muy limitada. El consumo de alimento en las aves, además del estímulo visual, depende de mecano receptores ubicados en el pico que se estimulan con un cierto tamaño de partícula. Los mejores resultados en pollos de engorde y aves en crecimiento se obtienen con una molienda que genere partículas entre 0,8 a 1,1 mm (800 a 1100 micrones), sobre todo cuando el alimento es en harina, pues aumenta el tamaño y la actividad de la molleja, promoviendo una acción antibacteriana, un reflujo alimenticio y una mayor motilidad intestinal, lo que aumenta la digestibilidad de los nutrientes y reduce la humedad de las heces.
El tamaño ideal de partícula antes mencionado no es el más apropiado para generar una óptima calidad del pellet; normalmente 500 a 700 micrones facilitan una buena peletización. Sin embargo, si el pellet se desarma el ave difícilmente comerá las partículas finas, por lo tanto es importante un mayor tamaño incluso cuando el alimento se peletiza. En el caso de granos duros, como el maíz, se obtiene un mejor desempeño en pollos de engorde cuando la molienda para peletizar se mantiene con partículas entre 800 y 1100 micrones.
En gallinas en postura se debiera usar un grano molido grueso al igual que el 70% del carbonato de calcio (3 a 5 mm) para permitir que la ponedora seleccione los diferentes ingredientes (nutrientes) a diferentes horas del día.
El pesaje de ingredientes muchas veces resulta en el cuello de botella de la fabricación de alimento debido a la falta de balanzas. Las balanzas y los sistemas de dosificación líquida necesitan de frecuente calibración para asegurar la precisión de las cantidades que se están adicionando. El desempeño productivo de las aves se ve afectado cuando las balanzas están descalibradas y no existe un programa establecido de calibración o cuando las balanzas son inadecuadas para el peso requerido.
Dependiendo del tipo de ingrediente y la sensibilidad de las aves, se acepta una desviación máxima en la precisión del pesaje; que en el caso de los ingredientes mayores es de ± 3.0%; para el carbonato de calcio y fosfato es de ± 1.5% y para la sal y el bicarbonato es de ± 1.0%. En el caso de los líquidos como aceites y melaza la desviación del pesaje no debe pasar de ± 3.0% y para el cloruro de colina y aminoácidos en forma líquida ± 1.0%. Muchas veces los estándares de la fábrica son más estrictos que lo que detecta o le afecta a las aves.
Normalmente en las fábricas de alimento existe una operación de micro mezclado donde se pesan aditivos, vitaminas, minerales trazas y medicamentos antes de incluirlos en la mezcladora grande. La tolerancia de precisión en el pesaje de estos micro ingredientes desde el punto de vista de las aves es de ± 30 gramos cuando se usan 2.5 kilos o menos y de ± 1.5% cuando el uso es mayor de 2.5 kilos.
Mezclado y secuencia de fabricación
El diseño, mantenimiento y limpieza de la mezcladora son fundamentales para producir un alimento adecuado. La uniformidad de la mezcla se mide a través de un test donde idealmente el coeficiente de variación se encuentre entre 5 a 10% y debiera realizarse por lo menos dos veces al año. Desde el punto de vista del desempeño de las aves, la uniformidad de la mezcla puede tener un coeficiente de variación de hasta un 10% sin que se detecten efectos negativos. Una vez más las especificaciones de la fábrica en este caso son mucho más rigurosas.
La secuencia y tiempo de mezclado son muy importantes. Con la mezcladora funcionando, se inicia el proceso adicionando los macro ingredientes (30 segundos), después se adicionan los micro ingredientes (10 segundos) y se mezclan por 60 segundos; posteriormente se adicionan los líquidos (30 segundos) para una mezcla final de 60 segundos y una descarga de 20 segundos; lo que totaliza un tiempo ideal de mezclado de 3 minutos y medio. Es recomendable separar la adición de líquidos, adicionando primero metionina, colina, etc. y posteriormente el aceite o la grasa.
Es de suma importancia planificar la producción diaria, especialmente si en la fábrica se manufacturan alimentos para diferentes especies animales. Se debe planear la producción en base a una secuencia lógica que evite tener que limpiar el sistema entre alimentos.
Alimentos que contienen coccidiostatos como diclazuril, lasalocida, maduramicina, monensina, narasina, nicarbazina y salinomicina son los más críticos en cuanto al próximo alimento a fabricar, pues residuos de algunos de estos medicamentos pueden afectar a caballos, perros, conejos, pavos, gallinas y reproductoras de pollos.
Textura del alimento
Idealmente la textura del alimento debiera ser mini-pelet o quebrantado en el pre-inicio, quebrantado en el inicio y peletizada en las siguientes dietas del pollo de engorde. La peletización mejora ganancia de peso y eficiencia alimenticia (5- 10 %) dependiendo de la calidad del pellet, de la grasa adicional y del uso o no de ingredientes de baja densidad. Si se logra llegar con una dieta 100% pellet al plato del comedero, su efecto en el desempeño productivo del pollo equivale a 180 kcal/kg adicionales de energía metabolizable a la misma dieta en harina
Las dietas bien peletizadas aumentan consumo, mejoran la fluidez y la higiene del alimento, así como la conversión alimenticia; reducen el desperdicio y el gasto energético de los pollos; e inclusive el costo de transporte. Todas estas ventajas se obtienen siempre que se logre llegar con 60% o más alimento peletizado al plato del comedero. Si la cantidad de pellets frente a las aves no es más de 50% entonces, dependiendo del costo energético en cada país o localidad, es más rentable hacer el alimento en harina con adición apropiada de grasa o aceite.
Despacho y distribución del alimento
Es crítico asegurar que el alimento que se va a despachar esté bien identificado; si es a granel en el silo correcto de la fábrica y en el compartimento cierto del camión para evitar errores en el destino final. Un alimento puede perder su calidad durante el traslado desde la fábrica de alimento hasta el comedero por mal almacenaje en la granja o por destrucción de su textura debido a inadecuado manejo del sistema de comederos.
Conclusión
Es prácticamente imposible saber con absoluta certeza que están comiendo las aves; por lo tanto tenemos que conocer muy bien las materias primas con las que estamos formulando, cuidarlas durante su almacenaje, formular adecuadamente, manufacturar el alimento lo más cercano a la formulación y alimentar eficientemente a las aves para tener una mejor idea de lo que realmente están comiendo y poder relacionarlo así con el desempeño productivo.
Es siempre recomendable que el nutricionista comparta con el personal técnico encargado de la fabricación del alimento los puntos críticos de la manufactura con mayor incidencia en la productividad de las aves.
Referencias
- Dale, N. 2002. In vitro and in vivo procedures in quality control programs. World’s Poultry Science Journal 58:15-21
- Goh, W and Gaytan, I. 2016. Ensuring homogeneity and recovery of liquid additives in feed. Asian feed magazine. August/September 30-33
- Jacobs, C.M., P.L. Utterback and C.M. Parsons. 2010.Effects of corn particle size on growth performance and nutrient utilization in young chicks. Poultry Science 89:539-544
- Penz, A.M. 2012. Benefits of coarse particles on broiler gizzard. All about feed. 20:17-19
- Subramonian, R. and Lasap, S. 2016. Effect of raw materials on feed pellet quality. Asian Feed Magazine. February/March p 33-35
- Teeter, R. and L. McKinney. 2003. The caloric value of pelleting. Poultry international. December p 40-46
- Zaefarian, F., M.R. Abdollahi and V. Ravindran. Particle size and feed form in broiler diets: impact on gastrointestinal tract development and gut health. 2016. World’s Poultry Science Journal 72:277-290
- Zaviezo, D. 2012. Usted sabe que están comiendo sus aves ? Memorias XIII Seminario internacional de patología y producción avícola. Viña del Mar, Chile. p 49-56
- Zaviezo, D. 2014. Relación entre nutricionista y fábrica de alimento. Memorias IX Seminario internacional en ciencias avícolas. Santa Cruz de la Sierra, Bolivia.