Cuando hablamos de secado podemos usar también el concepto del triángulo de oro: infraestructura – operación – información.
En infraestructura avanzamos desde las viejas máquinas estáticas, a las rotativas, a las de flujo continuo. Décadas atrás aún se usaban las viajas Matiasi (tecnología de origen americano), tiempo después tuvimos secadoras con influencia europea, las históricas eureka (de caballetes) y las Margaria e Iradi de Columnas. Para granos especiales (maní – arroz) se desarrollaron tecnologías especiales, siendo Agrimaq pionera en el tema.
Margaria con recuperación de calor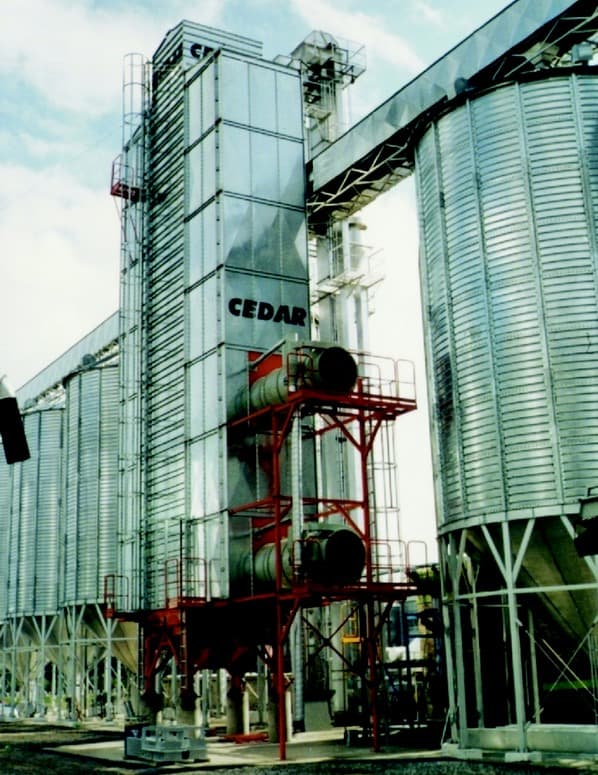
Tecnología superadora fue la Cedar, que conquistó también mercados externos y más recientemente la Mega, que introdujo el sistema superador de columna de flujo mixto. Paralelamente se fueron fabricando secadoras con más capacidad, con posibilidad de ampliar, fáciles de transformar a todo calor y se desarrollaron sistemas de monitoreo y automatización, inspirados en sistemas Canadienses y americanos. Tengo presente mi visita a farm fans una de las fábricas más importantes de secadoras, situada en Indianápolis, mientras nuestras secadoras tenían 1 censor la americana contaba con 50, mejorando notablemente la operatividad de la secada. Oportunamente con la crisis del petróleo algunas fábricas mejoraron su eficiencia energética incorporando recuperación de calor, aislación térmica, mejorando los caudales de aire. Los países de la región tienen realidades bien diferentes en cuento a los costos energéticos. Hace un par de décadas Argentina pasó al GLP y donde era posible Gas natural, Brasil usa casi exclusivamente leña, etc.
Con el sistema de columna mixta Argentina dio un paso al frente en el mundo que tradicionalmente discurría sobre ventajas y desventajas de las secadoras de columnas y de caballetes. Cuando hablamos de infraestructura también debemos considerar los sistemas de carga y descarga y la limpieza que normalmente va de la mano con el secado. Aquí podemos mencionar 2 temas, uno referente al sistema de prelimpieza, en el cual Argentina es líder, no confundir prelimpieza con limpieza previa, en muchos países se habla de prelimpieza y en realidad es el pasaje por zaranda antes del secado. De este tema ya hablamos bastante, si zarandeamos antes de secar la eficiencia de la secadora aumenta, pero nos encontramos con residuos de limpieza que deben procesarse rápidamente, para la operatividad general de la planta resulta mejor la prelimpieza de todo lo que entra y la limpieza después del secado (si esta fuera necesaria), incluso muchas plantas optaron por colocar la zaranda debajo de la secadora para evitar un equipo de carga adicional. Otro tema se refiere al clásico ladrón o caño rebalse, que vemos que en muchos casos descarga en la tolva de recepción, disminuyendo la capacidad de recibo.
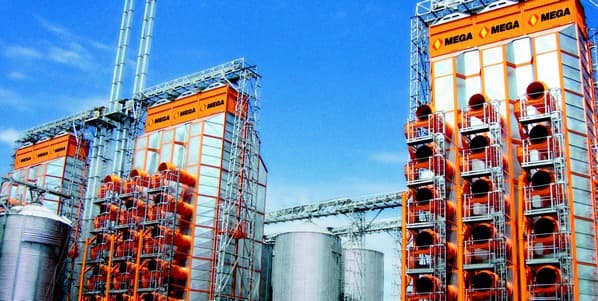
Laoperación, es otro aspecto fundamental, hasta el día de hoy tenemos manejos de secadoras continuas como si fueran estáticas. La falta de sistemas de monitoreo (sensores) y el desconocimiento de los principios de secado, así como la no instrumentación de planillas de control, llevan a problemas serios. Cuando existen limitantes en la clasificación y segregación inicial y reciben y mezclan en la tolva o en los silos humedades diferentes, se pierde la posibilidad de trabajar eficientemente. El resultado será de una gran amplitud de humedades en torno a lo deseado, generando 2 tipos de problemas, inestabilidad en la conservación posterior (grano muy húmedo) y sobresecados con daño más o menos severo a los granos. Las secadoras no tienen que aumentar las diferencias de humedad entre lo que entra, mas tampoco tienen mucha posibilidad de disminuir estas diferencias. Por eso la buena clasificación inicial, así como la prelimpieza, abren las posibilidades de un buen manejo. Se discute muy frecuentemente cual es la temperatura ideal del aire de secado, y poco se habla de la temperatura a la que llega el grano o la velocidad de extracción de humedad. La medición de la temperatura del aire servido es un buen indicador de lo que está pasando en el secado. Si el aire sale más caliente que lo normal, puede indicar un sobresecado o un principio de incendio. Décadas atrás se difundió la tecnología desarrollada por Foster y Makensi (Dryeration), la cual no fue bien asimilada en nuestra región, sin embargo los sistemas llamados de In Bim Cooling (secado combinado) puede ser usados con buenos resultados en casi todas las instalaciones, siempre que se refuerce un poco el sistema de aireación. El secado todo calor permite mayor eficiencia, rendimiento, economía y calidad.
El secado es sin dudas la práctica más costosa de la post-cosecha, por esa razón es menester siempre tratar de optimizarla, ajustando los parámetros operacionales e Implementando las mejores tecnologías disponibles.
La información es el tercero y fundamental lado del triángulo de oro. La gran mayoría de las secadoras carecen de cuenta horas, y por lo tanto se dificulta conocer cuánto tiempo trabajó (y relacionar esto con los rendimientos y consumos), casi ninguna planta realiza la medición de eficiencia energética, un calculo fácil de hacer, cuantas kcal se requieren para evaporar un kg de agua, este dato con la consideración de la calidad es el único válido para saber si estamos secando bien. Los cálculos de costos operativos, metodología que desarrollamos hace varios años, tampoco son de uso frecuente.
Otro tema relevante sobre el que a nivel continental hay mucha confusión es sobre el cálculo de las mermas, cada país y a veces cada región o empresa establece sus fórmulas de cálculo.
Resumiendo podemos dar algunas recomendaciones básicas:
- Mantener la secadora y máquinas conexas en buenas condiciones de mantenimiento.
- Fundamental disponer de sistemas de muestreo representativos y buenos equipos de determinación de humedad.
- Realizar la prelimpieza de la mercadería a secar.
- Clasificar o regular la entrada de grano húmedo dentro de rangos razonables (2 %).
- Disponer de sensores de temperatura del grano y del aire servido.
- Instalar cuenta horas.
- Privilegiar los combustibles más limpios y de mayor eficiencia.
- Efectivizar los planillas de control. Condición – rendimiento – eficiencia y costos.
- Tender al uso del todo calor.
- En las regiones más frías usar la aislación térmica.
Y como recomendación final, tratándose de la práctica que requiere la mayor inversión y gasto y que tiene un potencial de daño importante, siempre estar atento a ver que se puede mejorar y trabajar en la capacitación del personal.