Decidí escribir este artículo a raíz de un caso concreto, en el que me pidieron que diera mi opinión sobre la compra de ventiladores para refrigerar a las vacas a lo largo de la línea de alimentación de una determinada explotación lechera. Este sitio tenía 240 metros de largo y se utilizaba para alimentar (y refrigerar) a 320 vacas.
El propietario de la explotación lechera tenía dos propuestas para instalar ventiladores en la zona de alimentación y combinarlos con aspersores. El primer ventilador tenía un diámetro de 50” con un motor de 1.5 hp y transmisión por correa, con un consumo de energía de 1.1 kWh. Para lograr la velocidad de viento deseada de 3 metros por segundo, los ventiladores debían instalarse a 9 metros de distancia. El precio de este ventilador era de $500. El segundo ventilador tenía un diámetro de 63”, con un motor de 1 hp y operación directa del motor, con un consumo de energía de 0.75 kWh y recomendaciones de instalación a una distancia de 12 metros entre un ventilador y el otro para lograr la velocidad de viento deseada, el precio de este ventilador era de $1,200.
La gran diferencia de precio entre los dos ventiladores llevó al dueño de la granja a preferir comprar los ventiladores más económicos. Si bien, para ventilar el pesebre con los ventiladores más económicos, se requieren 27 ventiladores, pero a un precio de $500 por ventilador, esto es una inversión de $13,500. Elegir los ventiladores más caros requeriría la compra de solo 20 ventiladores, pero la inversión es de $24,000. Una diferencia de 10,500 dólares es significativa y el propietario de la granja tiene muchas cosas que hacer con esa cantidad de dinero.
Antes de tomar una decisión final, el propietario de la granja decidió consultarme sobre el asunto. Le expliqué que, efectivamente, la diferencia en la inversión es grande, pero la decisión debe tomarse solo después de calcular el costo total de refrigeración, que incluye por un lado el costo de inversión en el equipo de refrigeración (en nuestro caso los ventiladores) pero también el costo de funcionamiento del equipo a lo largo del tiempo. A veces hay sorpresas, le dije y nos pusimos a calcularlo juntos.
En la primera etapa, definimos la duración de la operación de refrigeración en la granja, que es de 180 días al año. En la segunda etapa, calculamos la duración del funcionamiento de los ventiladores en la zona del pesebre a lo largo del día, y esto fue de 10 horas. Por lo tanto, cada ventilador funciona 1800 horas al año. En esta etapa, pasamos a calcular el consumo eléctrico para enfriar las vacas a lo largo del pesebre dado con cada uno de los ventiladores, esto para el primer año de funcionamiento, y posteriormente para cada uno de los siguientes seis años (cuando estimamos siete años de existencia del ventilador). Los resultados de la comparación se presentan en la siguiente tabla.
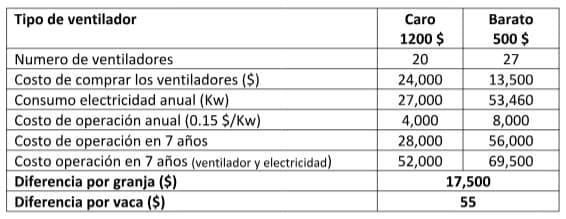
De la tabla se desprende que, a pesar del bajo precio del ventilador, lo más importante es su intensidad de ventilación (distancia entre ventiladores) así como la eficiencia energética del motor (consumo eléctrico por hora de funcionamiento). En nuestro caso, los ventiladores más caros tenían mayor potencia de ventilación, lo que nos permitió conseguir la velocidad de viento deseada con menos ventiladores, y no menos, motores más eficientes (funcionamiento directo frente a funcionamiento por correa), lo que nos permitió conseguir el resultado, gastando menos electricidad.
A la hora de hacer el cálculo, este debe hacerse para el número de años que estará en funcionamiento el ventilador. Si comparáramos el resultado al final del primer y segundo año, veríamos una ventaja para los ventiladores más baratos, ya que el precio del ventilador como parte del gasto total era relativamente grande. A partir del tercer año y hasta el final de los siete años, la tendencia se invierte y lo caro se vuelve más barato.
Por tanto, el ventilador más barato no siempre es el más viable económicamente.