Este informe es una simple recopilación de conceptos básicos de instalaciones y equipamiento de granjas porcinas en confinamiento. El objetivo de este artículo es poder visualizar el funcionamiento de este tipo de salas como así también brindarle al lector y/o productor porcino una información sintética de cómo son las instalaciones, equipamiento y herramientas a utilizar en el interior de las mismas. Como profesional de la Ingeniería en lo que se refiere a proyectos de construcción de granjas porcinas, me pareció apropiado en este caso, ilustrar el artículo con algunas imágenes de interiores muy requeridas por nuevos y jóvenes productores, junto con diversos implementos básicos de funcionamiento. Espero que este documento permita esclarecer ciertas dudas, fundamentalmente para los lectores que tengan intenciones de iniciarse en este tipo de actividad. Muchas gracias por leerme y estoy a vuestra disposición para lo que corresponda.
Premisa
El confinamiento intensivo porcino se subdivide en dos tipologías fundamentales:
• Intensivo de Reproducción
• Intensivo de Crecimiento
Tal clasificación puede también en algunos casos ser diferente, ya que un confinamiento de reproducción puede prever también el engorde de animales por lo tanto se habla de confinamiento a ciclo cerrado, mientras que en los casos que el destino del confinamiento sea único (reproducción o crecimiento) se habla de granja en confinamiento a ciclo abierto. Es evidente que entre los dos extremos existen una serie de situaciones intermedias que vienen denominados confinamientos a ciclo parcialmente cerrado y abierto.
Granja Intensiva de reproducción
El ciclo productivo relativo a este tipo de confinamiento prevé las siguientes operaciones:
1) Recepción de cerdas de reproducción.
2) Inseminación, gestación y parto.
3) Expedición y transporte al Sector Crecimiento.
Recepción de Cerdas Reproductoras
Las cerdas de reproducción vienen adquiridas de criaderos especializados en selección de animales reproductores o seleccionados en el interior de la granja.
Las cerdas seleccionadas en el interior de la misma, vienen reunidas en la zona de espera en calor listas para ser inseminadas.
Las cerdas que provienen de otras granjas mediante traileres especiales son destinadas a las salas de espera o al “local cuarentena”.
La descarga de los animales se realiza mediante apropiadas rampas móviles que vienen acostadas y orientadas a la puerta de descarga y mediante el ingreso de un operador sobre el trailer, las cerdas se las hace descender y puestas en movimiento se las dirige hacia el interior de los box de la sala de espera o de la sala enfermería.
Desplazada la rampa de descarga, el trailer es llevado a la zona de lavado y desinfección para poder realizar un nuevo transporte. (Figura 79 – rampade descarga para cerdos).
Rampa de descargaLa sala de espera es normalmente el lugar dónde se realiza la inspección de los animales y el control contumacial por parte del veterinario. Este control viene efectuado sobre los animales no tabulados en box, además un operario recibiendo explicaciones del médico veterinario aísla los animales a inspeccionar entreteniéndolos con herramienta apropiada o encerrándolos en box predispuesto para ello.
En esta zona los animales que presentan signos evidentes de enfermedades, traumas o debilitados son separados para efectuarles tratamiento terapéutico.
Pasado el período de cuarentena las cerdas- madres son trasladadas al sector gestación en jaulas individuales (figura 80) en espera del primer estímulo (calor).
Sector Gestación en jaulas individualesEn esta zona independientemente de la técnica de fecundación utilizada viene efectuada diariamente la estimulación con el verraco (padrillo), el cuál es conducido por un operario entre las jaulas, esta operación tiene una singular importancia en estimular calor en los animales gracias a la gran cantidad de feromonas producidas.
Inseminacion, Gestación y Parto
La inseminación puede ser natural (hoy por hoy solo en pequeñas realidades y en algunos animales) y artificial.
La inseminación natural prevé que la cerda sea transferida asu correspondiente jaula (fig. 81) para ser montada de parte del padrillo.
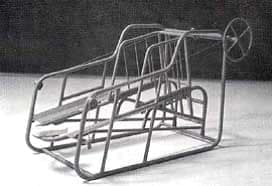
(Fig. 81 caballete de monta natural de parte del padrillo)
La inseminación artificial se compone de algunas operaciones que pueden ser esquematizadas de la siguiente manera:
- Extracción de semen del padrillo.
- Análisis del semen extraído y su disolución en pequeñas dosis.
- Inseminación de la cerda.
Extracción de Semen
El padrillo, al terminar la ronda de estimulación delante de las cerdas en el sector gestación, viene dirigido por un operario hasta el local donde hay una especie de caballete que lo llaman “potro fijo” o “potro móvil” (que simula una cerda) sobre el cual se hace montar el padrillo (fig. 82).El operario recupera el semen del mismo mediante una vagina artificial a temperatura controlada (aprox. 37 – 38 ºC) que viene inmediatamente transferida al local dónde se efectúa el análisis del semen.
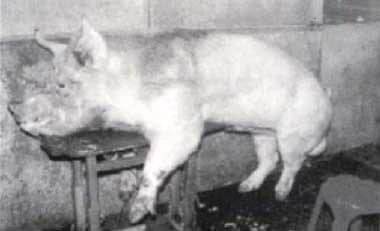
(Fig. 82 – “potro fijo” para extracción del semen)
Analisis del Semen Extraido y su Disolución en Pequeñas Dosis
Con el semen extraído se preparan algunos vidrios para observar mediante el microscopio. Viene analizada la vitalidad de los espermatozoides y su movilidad.
En función de estas características y de la concentración relevada en el semen, se preparan, mediante disolución con líquidosfisiológicos apropiados las dosis individuales para inseminar las cerdas.
Inseminación de la Cerda Mediante correspondientes catéteres desechables ligados a la bolsa de semen, el operario efectúa la inseminación a la cerda (fig. 83).
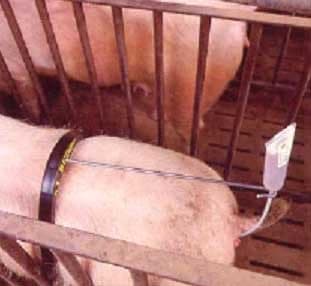
(Fig. 83 – Inseminación Artificial)
Confirmada la gravidanza en las cerdas, estas vienen transferidas a los box múltiples teniéndolas allí hasta una semana antes delparto, dónde serán transferidas a las salas correspondientes.
Sala de Parto
Es un local equipado con diferentes jaulas (fig.84) en grado de albergar la cerda –madre hasta el periodo de lactación (21 – 28 días).
La cerda-madre realiza el parto sin necesidad de asistencia por parte del operario, que interviene solo en caso de parto problemático.
La cerda-madre en esta fase es particularmente agresiva y protectora del nido, motivo por el cual cada eventual intervención por parte del operario en asistir a la madre o a los neonatos puede constituir un factor de riesgo.
Es evidente que en esta zona del confinamiento se debe efectuar una correcta práctica higiénica, con limpieza y desinfección de las estructuras cuando las madres dejan la sala de parto para volver al sector gestación (para la estimulación de un nuevo calor).
En lo que concierne a la asistencia y cura de los neonatos-lechones se hace comentario en el punto “cura y tratamientos sanitarios” no tratado en este documento.
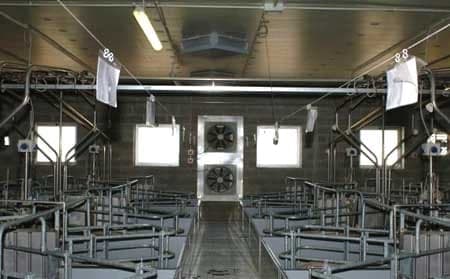
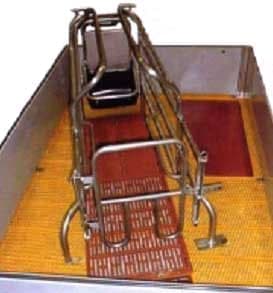
(Fig.84 – Jaulas y sala de parto)
Los lechones alejados de la madre vienen generalmente transferidos a la sala de destete o quedan en la misma ya que la cerda-madre como es apartada de dicha sala se absorbe tal función, en esta fase los lechones vienen vacunados. Los lechones destetados que llegan al peso de 30 – 40 kg, en función del management de la granja quedan disponibles para ser expedidos o transferidos al sector engorde.
Expedición - Transporte
Para la expedición de los animales se procede a la carga sobre un trailer utilizando la rampa-móvil de carga (fig.79) a excepción de los movimientos que se realizan en el interior de las salas que se realizan concarros equipados o mediante corredores de movimiento (fig.85).
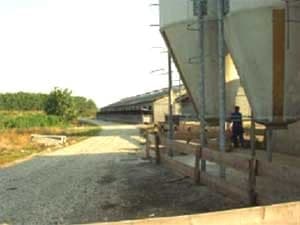
(Fig. 85 – Corredor de movimiento de animales)
En lo relativo a mover los animales muertos, los lechones son llevados manualmente cuando su peso es 20 – 25 kg y sucesivamente por medio de carros equipados utilizados para la carga y para los movimientos internos de cerdos muertos de peso elevado, madres, capones etc. (fig.86).
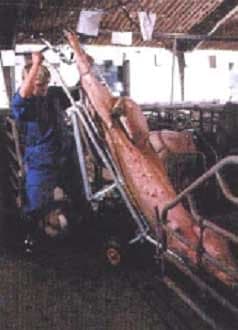
(Fig. 86 – Carro para la carga y transporte de capones muertos)
Salas de Engorde
Recepcion de Animales
Los animales son transferidos desde el sector destete (fig. 87) al sector engorde (fig.88) o llegan transportados en trailer. (Fig. 89)
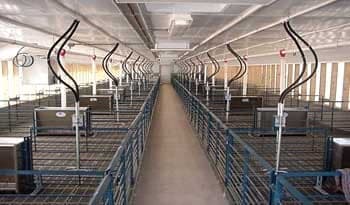
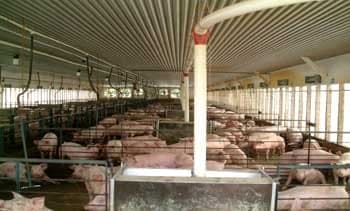
(Fig. 87 – Sector Destete) (Fig.88 – Sector Engorde)
Se procede la descarga de la misma forma como se realizó con las cerdas en el sector gestación.
Los animales en este caso son destinados al interior de las salas donde serán engordados hasta el peso de faena previsto (160 kg para la producción de jamón o hasta el peso de 100 – 120 kg para el cerdo de carnicería).
Los lechones serán subdivididos en grupos más o menos homogéneos en función de la edad y del peso, encerrados en el interior de los box.
Un operario se ubicará sobre el trailer y otro en el interior de la sala para dirigir los mismos hacia los diferentes box.
Terminada la descarga, el trailer es llevado a la playa de lavado y desinfección para poder efectuar otra carga similar.
En los primeros días de confinamiento los operarios verifican el estado de los animales junto al veterinario, se establece la estrategia alimenticia y de profilaxis como así también la terapia a utilizar.
Generalmente los operarios (antes que los animales estén juntos en el box o apenas son ingresados) proceden a esparcir por tierra en forma manual alimento balanceado en forma de harina, a los fines de educar a los animales respecto de un área del box como zona de reposo, delineando una zona de defecación o utilizando aquella presente (realizada normalmente sobre pisos ranurados).
De esta manera se procede entonces a la normal gestión alimenticia que en casi todos los casos se prevé alimentación liquida con distribución automatizada en los comederos.
Durante el ciclo de engorde(en algunos casos) los operarios suelen reunir en diferentes box los animales en mejores condiciones homogéneas. Tales operaciones (igualación) se efectúan un par de veces antes de la primera fase de crecimiento (50 – 60 kg) y al inicio de la fase de engorde (80 – 100 kg).
También en este sector del confinamiento se deben mover los animales muertos y aquellos que deben ser objeto de tratamientos terapéuticos.
El movimiento de los animales muertos se los realiza directamente entrando con los carros de la fig.86,alivianando con el carro de transporte; el cadáver viene transportado a un local destinado para este tipo de situaciones en espera de ser recuperado por parte de empresas autorizadas para estos casos.
Expedición Una vez que se llega al peso de faena previsto, los animales son cargados sobre el trailer mediante la rampa-móvil (fig.79).
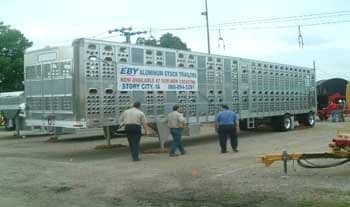
(Fig. 90 – Trailer de transporte)
Un operario entra en el box de animales a cargar, mediante dispositivos de conducción (paneles y látigo de plástico) los hace salir por el corredor que tiene salida a la rampa de acceso al trailer.
Normalmente un segundo operario que en algunos casos es el mismo chofer del trailer incita a los animales para que se desplacen por la rampa y subir al trailer.
Una vez completada la carga se efectúa el transporte a faena.
Gestión Alimenticia
La alimentación de los cerdos es la operación que mas se repite en el curso de una jornada en el ciclo de crianza.
Podemos analizar algunos aspectos principales que son relativos a:
1) STOCK Y CONSERVACION.
2) PREPARACION Y DISTRIBUCION.
1) Stock y Conservación
Los componentes utilizados en la alimentación de los cerdos, pueden ser en forma seca
(harina, pellet, etc.) o en forma líquida (suero de leche, aditivos, etc.).
Es evidente que el diferente origen de los componentes utilizados prevé una diferente forma de conservación y de stock.
Ocurre distinguir inicialmente en función del origen y naturaleza de los componentes, que pueden ser alimentos simples (harina de maíz, soja, etc.) y alimentos compuestos integrales listos para el consumo.
Los primeros son conservados en silos verticales (fig.93) y son movidos mediante tornillo sinfín (chimango) de transporte o con elevadores a tazas. Son componentes que pueden ser utilizados en la preparación de un alimento compuesto industrial para consumo por vía seca o también mezclados y movidos en suspensión mediante un vector líquido (agua, suero).
Los alimentos compuestos integrales son transportados al confinamiento mediante camiones equipados apropiadamente, se hace stock directamente en los silos verticales en fibra de vidrio (fig.93) o acero zincado mediante la utilización de tornillo sinfín (chimango) de descarga prevista sobre el trailer del camión.
Los alimentos simples vienen descargados desde el camión dotado de caja metálica de acopio directamente a la fosa de descarga.
Se trata de un acopio que tiene cota menor que la de descarga del camión, de allí con tornillo sinfín (“chimango”) se envía el producto (cuando se necesite) a los silos verticales en espera de su uso o de la trituración del producto si el mismo viene a granel y se utiliza como harina,(el maíz por ejemplo).
Algunos componentes (integradores minerales y vitamínicos) en forma seca, son retirados en bolsas colocados sobre pallets movilizados con carros elevadores.
Los componentes individuales acopiados en los silos verticales pueden ser mezclados directamente en el momento de utilización para la alimentación de los animales o también los alimentos simples pueden ser reunidos para formar compuestos industriales. Este tipo de trabajo se realiza o tiene mayor difusión en Granjas Confinadas de notables dimensiones en grado de amortizar en poco tiempo los costos asumidos en la realización de una verdadera fábrica de alimentos balanceados.
2) Preparación y Distribución
La preparación del alimento para cerdos se puede realizar de diferentes modos en función de la forma en que es suministrado el alimento.
La alimentación de cerdos por lo tanto puede ser efectuada bajo la forma “ en seco” o bajo la forma “líquida”.
La primera es casi siempre utilizada como complemento a la leche materna, por ejemplo en el último periodo de lactación.
En esta fase, dadas las cantidades consumidas,el alimento es distribuido manualmente por el operario que mediante un balde y paleta llena los comederos de los lechones presentes en cada jaula de parto.
En el sector destete, se puede adoptar al alimento líquido como integrador o como alimento principal.
La elección de una forma de alimentación u otra es en realidad un tema de gestión.
Alimentación en forma “ en seco”
La distribución del alimento seco, puede realizarse manualmente mediante carro y balde o prever un sistema automatizado para la distribución.
En el caso de distribución automatizada se utilizan particulares accesorios que consisten en espirales o cadenas de transporte, movilizan el alimento seco desde el silo de stock (fig.93) directamente al interior de los comederos. El sistema de transporte tiene su inicio en la apertura de descarga del silo teniendo derivaciones hacia todos los comederos presentes en la salas, teniendo el sistema de retorno su punto final en el silo de partida. (fig. 91)
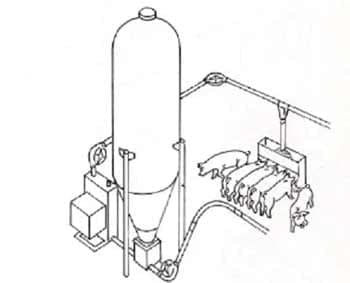
(Fig. 91 – Esquema de sistema de transporte para alimento seco)
Tales accesorios de transporte son accionados mediante motores eléctricos que proveen el movimiento de discos unidos entre si mediante un cable (fig. 92) en el interior de una cañería de PVC o acero inoxidable, de esta manera el alimento se desliza por la cañería depositando el mismo en cada comedero, que en su momento han sido ya vaciados por los animales.
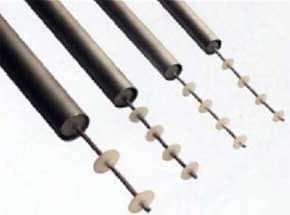
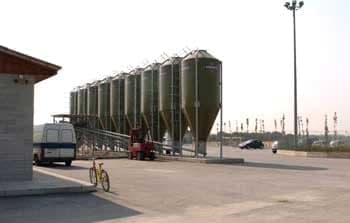
(Fig. 92 – cables y tubos de transporte para alimento seco). (Fig.93 – stock de alimentos en silos)
Alimentación en forma “liquida”
En este caso el alimento en seco es movilizado hacia los comederos suspendidos en un medio líquido como el agua o el suero de leche.
Esta forma de alimentación prevé la predisposición de un verdadero y propio local de preparación del alimento (broda) o cocina, dónde se instalan todas las maquinas que componen el sistema de alimentación.
Los varios componentes del sistema deben ser correctamente integrados y coordinados entre ellos para lograr un correcto funcionamiento.
a) Sistema de dosificación.
b) Tanque y sistema de preparación – mezcla alimenticia (broda).
c) Bombas de distribución.
d) Entubado.
e) Válvulas de distribución.
El sistema de dosificación reviste un rol esencial en la instalación ya que se determina la cantidad de los componentes en forma individual para cada ración.
Los tanques de preparación (fig. 94) se construyen en acero inoxidable, PVC o fibra de vidrio (VTR), de diferentes formas (circular, cúbica o elíptica)dotadas de 3 o 4 pies de apoyo, colocados sobre celdas de cargas y vinculados al sistema de tara.
Estos tanques pueden ser de tipo cerrado o abierto y están en comunicación directa con el tornillo sinfín (“chimango”) de descarga de los silos de materia prima, a través de los cuales reciben los componentes individuales de la ración, previa aceptación digital realizada en la computadora.
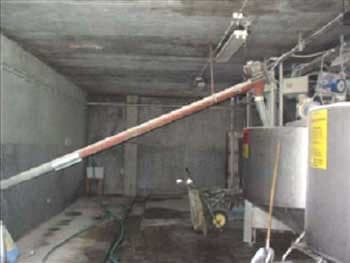
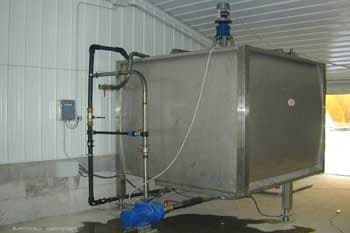
(Fig. 94 – Tanques de acero inoxidable de preparación y distribución de mezcla alimenticia (broda))
La capacidad de estos tanques es limitada, variable de 2 a 5 toneladas, equipados con sistema de agitación para obtener la homogeneización de la mezcla (broda) ya sea en la fase de preparación como en la distribución.
La mezcla (fig. 95) representa un aspecto de gran importancia en lograr la homogeneidad de la misma en tiempo y forma, garantizando la correcta distribución de la ración en la boca del cerdo, es esta la causa que motiva numerosas propuestas por parte de los constructores de este tipo de sistemas que van desde la particular conformación de las paletas del agitador y su temporización, hasta la disposición de especiales deflectores en las paredes del mismo recipiente de mezcla.
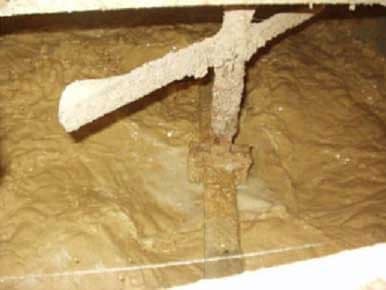
(Fig.95 – Mezcla Alimenticia (broda) en el interior de un tanque de preparación)
En el caso que venga previsto el empleo de pastones ensilados (maíz, trigo, sorgo, etc.)se debe disponer de un pre-tanque de mezcla, que permite realizar en el mismo una primera mezcla del pastón con agua, de esta forma se puede transportar el producto desde el silo a la cocina (local de mezcla) mediante bombeo e introducirlo fácilmente en el tanque de mezcla alimenticia.
Terminada la fase de preparación del alimento, este es movilizado mediante entubado y válvulas de distribución directamente a los comederos del confinamiento sin la asistencia por parte del operario, cuya función se limita solamente al control del funcionamiento de la instalación explicada.
Gestion de Efluentes Zootecnicos La gestión de los efluentes zootécnicos producidos en el confinamiento porcino es variable en función de la tipología utilizada.
Estos locales, se caracterizan generalmente por la producción de deyecciones, que son recogidas debajo de pisos ranurados previstos en toda el área del box o eventualmente en el área mas estrecha que ocupa la faja de defecación como queda evidenciado en la fig.96.
Actualmente se ha abandonado la tipología con pisos macizos (llenos) y faja de defecación con bloques auto-desmontables responsables de una notable disolución del material defecado, por ello se han desarrollado soluciones con fajas de defecación externa e interna siempre en pisos ranurados.

(Fig.96 - Sala Confinada con fajas externas e internas de defecación en pisos ranurados)
Otras soluciones contemplan la realización con pisos ranurados en todo el interior de las salas y la presencia de fosas de stock de deyecciones que se posicionan debajo de estos pisos (fig.97). Estas soluciones son las responsables de empeorar la calidad del aire “indoor”(interior), por este motivo no se permite en la actualidad este tipo de fosas, sino aquellas que se posicionan debajo de pisos ranurados pero su función es la de “vehículizar” las deyecciones.
Diferentes son las modalidades utilizadas para permitir un desplazamiento del fluido y el vaciado de las fosas. Entre estas posibles modalidades podemos recordar:
1) Vaciado por rebalse continúo.
2) Vaciado discontinuo a gravedad (vacuum system).
3) Vaciado por flushing.
4) Por agitación mediante rastrillo mecánico.
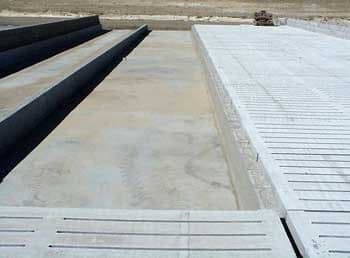
(Fig.97 – Fosa de vaciado y pisos ranurados de hormigón premoldeado)
1. Fosa de Movimiento de Fluido a Rebalse Continuo
Estas fosas contienen en uno de sus extremos una canaleta de altura variable (fig.98), altura dimensionada en función de la longitud de la fosa que permite mantener un estrato líquido de fondo sobre el cuál se desliza la masa sólida de defecación.
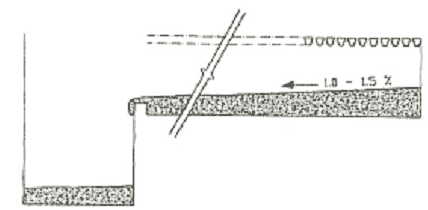
(fig. 98 – fosa con canaleta a rebalse continuo)
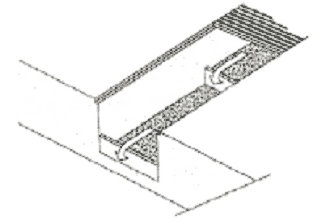
(fig.99 – fosa con canaleta a rebalse en cascada)
El fondo de la fosa es perfectamente plano (cota cero) y el funcionamiento de todo el sistema esta asegurado por las fermentaciones anaeróbicas que se instauran en el interior de la masa defecada y en particular de los gases desprendidos en forma de burbujas que movilizan en superficie las partículas sólidas inicialmente sedimentadas.
En los casos de grandes longitudes de fosa es conveniente realizar más canaletas pero en cascada (fig.99).
2. Vaciado Discontinuo a Gravedad (Vacuum System) Consiste en la realización de un verdadero desagüe con cañería de PVC (plástico reforzado) colocada debajo de la platea-fondo fosa (fig.100).La red de desagües está vinculada a la fosa mediante varios orificios de fondo (distribuidos uno cada 10 m2 aprox.).El sistema drenante está cerrado mediante una adecuada compuerta en acero inoxidable o PVC. De esta forma la masa defecada se acumula en la fosa hasta el momento de apertura de la válvula, que determina la rápida descarga del fluido defecado arrastrando todo material sólido remanente sin riesgo de entascamiento. Esto se debe al efecto de “aspiración” que se crea en los diversos orificios y el veloz escurrimiento del fluido por la cañería. En fase de construcción de este sistema se puede prever que la platea-fondo fosa sea plana o eventualmente con mínima pendiente hacia los orificios de descarga.
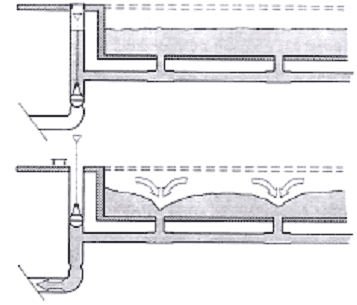
(fig.100 – Esquema de vaciado discontinuo a gravedad - vacuum system)
3. Vaciado por Flushing
Esta es una solución que permite agilizar el movimiento de la masa-liquido mediante una corriente generada por el flujo de líquido defecado en stock haciéndolo recircular en el fondo de la fosa. En realidad, el estrato de fluido (aprox. 8 – 10 cm.) que recibe las defecaciones producidas por los animales es periódicamente sustituido con limites de tiempo programados (12 – 24 hs), este estrato es reemplazado por el liquido defecado extraído del stock que se hace recircular desde la parte frontal de la fosa. La recirculación puede ser prevista extrayendo material de stock según tres modalidades:
a) Recirculación con utilización de material de defecación fresco.
b) Recirculación con utilización de material de defecación aireado en el stock.
c) Recirculación con utilización de material de defecación estabilizado en tanque de tratamiento. (fig.101)
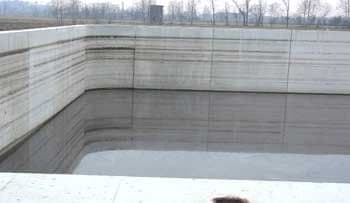
(Fig. 101 – Tanque de tratamiento de efluentes)
La recirculación utilizando material defecado fresco es el más simple de realizar: se efectúa la extracción directa del fluido de la cámara (depósito de descarga inicial) que se ubica generalmente a la salida de la sala que se le realiza el vaciado, de allí se bombea mediante bomba centrífuga hacia el fondo de la fosa a limpiar. Este trabajo por un lado tiene una notable simplicidad de realización y por otro, no es siempre efectivo en asegurar suficientes garantías sanitarias en el confinamiento, debido a la presencia de potenciales patógenos todavía inactivos que pueden ser inyectados otra vez al confinamiento, además viene comprometido la calidad del aire con desarrollo de olores y liberación de gases nocivos del fluido.
Mejores resultados se obtienen cuando se emplea material defecado aireado.
Este tratamiento consiste en imprimirle una intensa oxigenación al material defecado en stock, gracias a la incorporación de aire en cantidades suficientes para promover el desarrollo de fermentación aeróbica, se da mas velocidad biodegradable a la descomposición de la sustancia orgánica eliminando de esta forma la producción de compuestos malolientes.
Es evidente que el empleo de fluidos estabilizados permite reducir y además evitar los antedichos inconvenientes, superando también las contraindicaciones sanitarias.
En todo caso es buena norma la utilización de material stockeado sometido preventivamente a tratamiento de separación sólido – líquido.
Pueden además entrar en este tipo de solución de gestión, “las canaletas
múltiples” (fig. 102) y el piso ranurado “Lusetti” (fig. 103) dónde cada ranura corresponde a una canaleta en PVC.
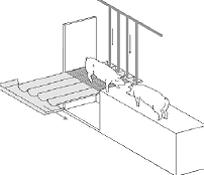
(Fig.102 – Fosa de movimiento con canaletas múltiples)
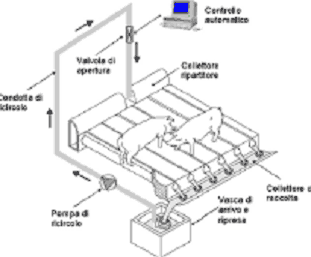
(Fig. 103 - Pisos ranurados “Lusetti”)
4. Por Agitación mediante Rastrillo Mecánico El desplazamiento de las deyecciones viene realizado mediante un rastrillo mecánico (fig. 104) instalado sobre el fondo de la fosa.

(Fig. 104 – Rastrillo mecánico instalado debajo del piso ranurado)
De este modo las deyecciones frescas son alejadas con mas seguridad, contribuyendo
al mejoramiento de las condiciones ambientales internas del confinamiento.
Las profundidad de la fosa para utilizar el rastrillo mecánico debe tener entre 30 y 40 cm., con la posibilidad de utilizarlo además cuando se realizan refacciones en locales ya existentes. Estas soluciones no están privadas de inconvenientes ya que vale la pena evidenciar lo siguiente:
a) El sensible aumento de los costos de construcción y de las intervenciones de mantenimiento que son frecuentes a causa del ambiente de trabajo particularmente agresivo.
b) Notable dificultad para cada eventual intervención de reparación no programada.